Background
Offshore wind generation is growing rapidly around the world.New solutions are needed to manufacture and install the needed capacity.
Offshore wind power generation is expected to grow rapidly over the coming decade, with the IEA projecting a 20% CAGR through 2030.
Investment in wind power generation has almost doubled by dollar value worldwide since 2020. This growth will require the installation of hundreds of floating substructures to support this growth in offshore wind generation.
As part of a project sponsored by the National Offshore Wind Research and Development Consortium (NOWRDC), we explored the applying techniques and expertise from offshore oil and gas platforms to supporting large wind turbines, with a particular focus on floating structures.
We analysed various types of structures, then investigated novel manufacturing and installation methods from the oil and gas industry that could be adopted by the offshore wind industry.
"The floating offshore wind turbine market is expected to grow from 121MW in 2021 to around 26,000 MW and 2656 floating units by 2035"

Analysis of Novel Platforms
The project started by examining a variety of novel platforms that are currently being used in the offshore oil and gas industry.
There are around 3,200 active offshore platforms in the Gulf of Mexico, including 21 Spars (e.g. Shell's Perdido in 2450m water depth) and and 30 TLPs (e.g. ConocoPhillips' Magnolia in 1425m water depth). Platforms types that we analysed included cell spars, moored buoyant towers, tension buoyant towers (TBT) and a mini-tension leg platforms (TLP).
We were able to drew on our team's deep experience working in the offshore oil and gas industry.
Site Conditions & Metocean Analysis
Analysis and design work was performed for two sites: California's Humboldt Bay BOEM Call Area (water depth between 500 and 1000m) and the Gulf of Maine (water depth of 150m). The designs assumed the use of an NREL 15MW “reference turbine”.
We carried out thorough site condition and metocean analysis in order to clearly and critically evaluate the options available. Analysis performed included wind profile and turbulence analysis, wind-wave misalignment, and modelling in Normal through Extreme Sea State conditions.
This analysis gave a solid basis on which to review the various platform configurations available, and to provide clear recommendations around choices, specifications, and installation options
Concept Analysis
Concepts were developed for 4 different types of floating platform; a cell spar; a tension-leg platform; a buoyant tower; and a tension buoyant tower. Each concept was thoroughly developed, including hydrodynamic modelling, sea state analysis, and mooring spread requirements.
Novel Installation
The study concluded by analysing two innovative cost saving concepts for installing floating offshore wind turbines on spars:
- An automated method of construction which allows local fabrication of the spar
- A simplified installation method not requiring complex specialist vessels
We submitted a concept which involved installing the tower and turbine on the spar horizontally, in-shore. The spar, tower and turbine would then be towed offshore, where it would be upended and towed to the installation site:
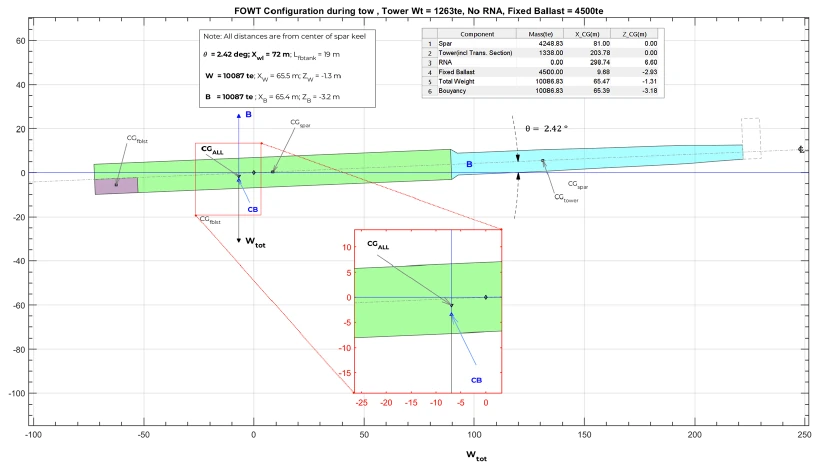
Detailed engineering modelling and economic evaluation indicate that this concept is an efficient and effective way of installing offshore wind turbines on floating structures.
Further Opportunities
Rapid growth in offshore wind requires unique concepts and solutions.The concepts we developed have the potential to revolutionize the offshore wind industry:
Site Analysis
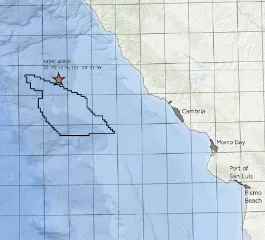
Advanced tethering techniques (e.g. subsea micropiles) adopted from the oil and gas industry increase the range of potential offshore wind sites.
In-shore manufacturing on barges provides further flexibilty along with economic opportunities for local areas.
Manufacturing
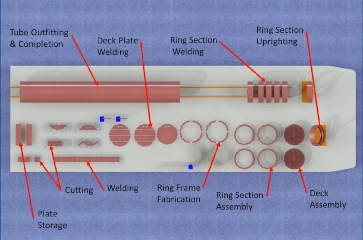
Onshore manufacturing is expensive and logistically complex. Mobile barge manufacturing can produce and install spars and towers rapidly and at lower cost.
The US requires multiple manufacturing facilities to meet the expected demand of 2600 floating offshore wind turbines by 2036.
Installation
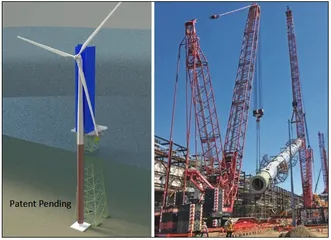
Increasing turbine diameters lead greater power generation and increasing efficiency, but introduce further logistical and installation complexity.
Installation on a spar via a self-erecting crane reduces sensitivity to metocean conditions, opening up installation windows and reducing downtime.